Для встановлення волоконно-оптичних ліній зв'язку часто потрібне створення роз'ємних та нероз'ємних з'єднань. І якщо в роз'ємних з'єднаннях існує безліч варіантів, то серед нероз'ємних все так чи інакше зводиться до зварювання оптоволокна. А для якісно виконаного зварювання критично важливим є правильне формування гладкої поверхні зрізу волокон. І тут не обійтися без сколювачів. Пропоную сьогодні розібратися в розмаїтті видів цього товару і специфіці їх вибору.
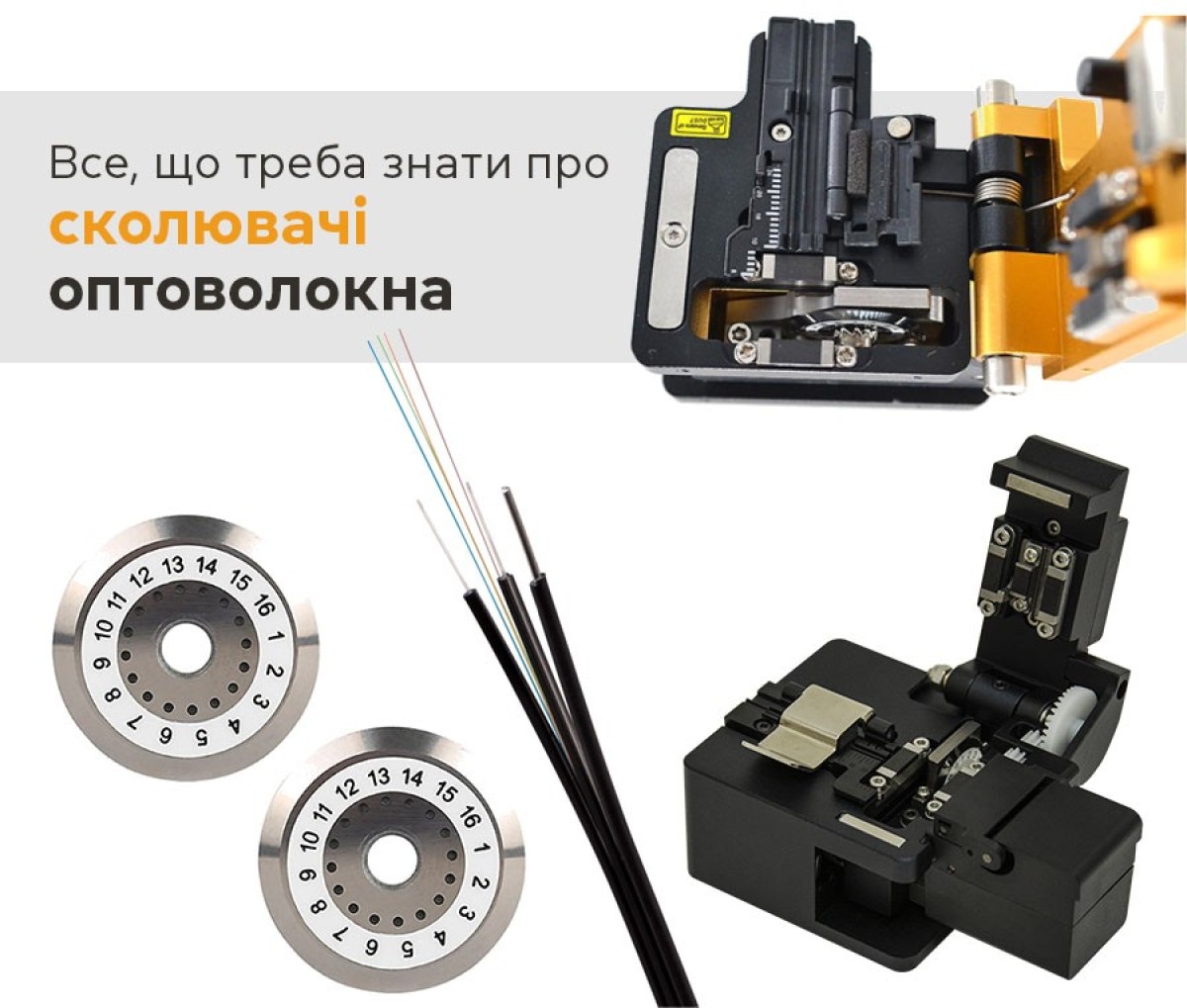
Принцип дії
Для простого пояснення можемо уявити кабель як стрижень, виготовлений з однорідного скла. Для того, щоб сформувати однорідний скол, поверхню необхідно спершу позначити неглибоким надрізом, а після цього робиться зріз за допомогою механічного тиску перпендикулярно волокну. Слід зауважити, що механічний тиск для відколу може бути реалізований трьома можливими способами:
- Зламом. Найпоширеніший варіант, що поєднує в собі простоту реалізації та якість результату.
- Розтягуванням. З точки зору теорії вважається найбільш якісним методом. Але на практиці мало відрізняється від попереднього варіанта і в реалізації складніший, тому застосовується рідше.
- Обертанням оптичного волокна. Це найменш якісний метод, тому застосовують його максимально рідко.
На малюнку нижче продемонстровано розподіл у циліндричному волокні напружень матеріалу для різних типів сколів
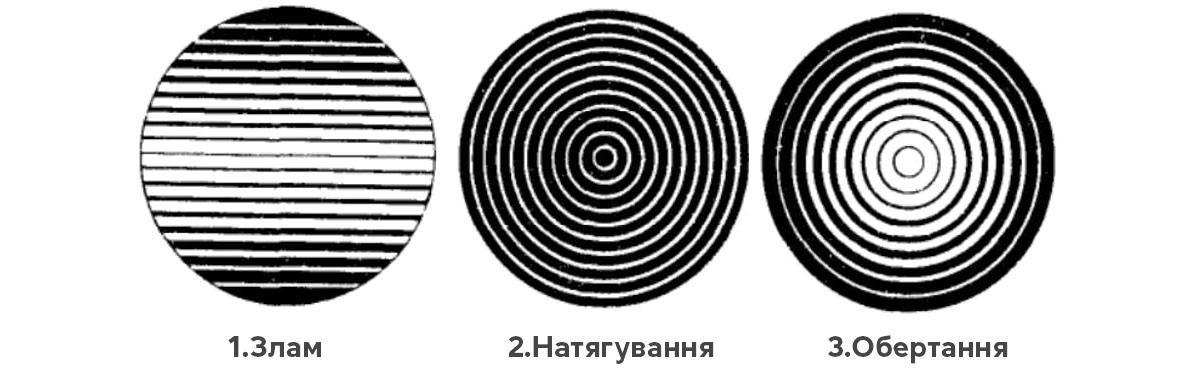
Важливо! Прецизійним вважається сколювач, що допускає не більше 1% відхилення поверхні зрізу від перпендикулярної площини.
У цьому тексті говоритимемо тільки про прецизійні інструменти, оскільки наявні на ринку неточні прилади у виконанні "прищіпок" і "ручок" нас не цікавлять - адже результат їхньої роботи вас точно не влаштує.
Варіанти формування насічки волокна
Первинний надріз може бути виконаний двома різними способами:
- Рублений. Реалізується за допомогою вібрацій кілогерцового діапазону. Дуже складний у практичному застосуванні, але якість результату виходить найвищою. Зустріти таке можна в лабораторіях і дослідницьких центрах.
- Лінійний різ. Для точного регулювання глибини насічки необхідно закріпити ділянку волокна, яку ми збираємося насікти, між двома бічними опорами і заздалегідь точно вирівняти їх за висотою. Під час руху ножа світловод, завдяки своїй гнучкості, трохи згинається вгору. Тиск, що створюється на різ, розраховується таким чином, щоб отримати насічку потрібної глибини.
Важливо, щоб у результаті отримана подряпина була досить великою, а подальший тиск призвів до тріщини у волокні. Зі зворотного ж боку, надто велика насічка буде просто дефектом на площині, яку неможливо буде якісно зварити.
Серед чинників, які є запорукою успішного результату, можна виділити як потрібний рівень гостроти самого ножа, так і правильне розташування і надійну фіксацію волокна в процесі різу. Не менш важливим буде і плавний хід різу з досить швидким і сильним натиском.
Цікаво: в процесі сколювання неминуче забруднення леза, а промивка, як правило, не дає помітного результату. Тому, ніж зроблений у формі диска і здатний робити поворот на кут у діапазоні 10°-30°, у разі забруднення або затуплення. Конкретне значення кута індивідуальне для різних моделей і позначене на лезі відповідними мітками.
Можна зустріти девайси як з ручним поворотом, так і автоматичним. Усе залежить від обраної вами моделі. Але в обох варіантах можливість обертання можна відключити спеціальним фіксатором. Тому в комплекті до приладу йде необхідний для фіксації шестигранний ключ.
Схема роботи
Схематично будову сколювача волокна зображено на малюнку нижче. У цьому виконанні людський фактор зведений до мінімуму, щоб уникнути помилок.
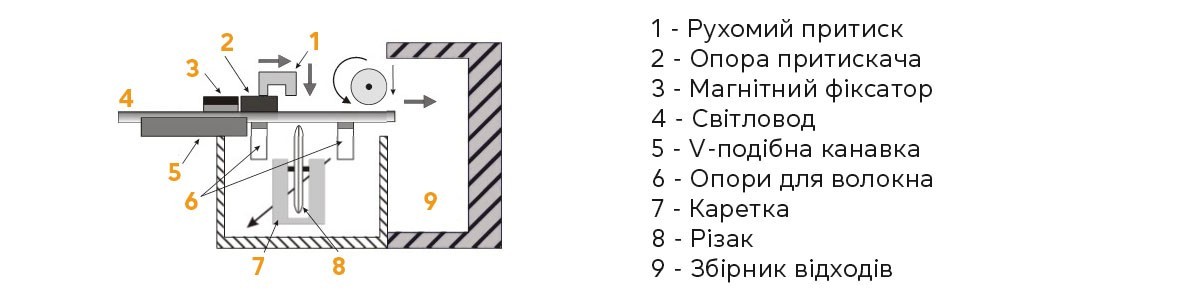
Процес сколювання може відрізнятися в різних моделях, але завжди складатиметься з ключових етапів:
- розміщення волокна в спеціальній канавці v-подібної форми;
- закриття верхньої кришки;
- відкриття кришки у відсік із відходами;
- плавний хід каретки різака;
- горизонтальний хід рухомого притискача з метою вигину волокна;
- обертання різака з метою підготовки до сколу;
- хід важеля на злам, захоплення волокна, обертання для видалення відходів;
- відкриття кришки і зупинка приводу каретки.
Зазначимо важливе значення кришки: в ній розташовані упори і важелі, які активізують весь процес у момент її закриття. У реальності ж усе має набагато складніший вигляд, з огляду на необхідність прецизійного вирівнювання волокон, точності розрахунку вигину волокна і глибини різу. Але для загального розуміння такого уявлення буде достатньо.
Ключові фактори вибору
На етапі вибору важливо врахувати кілька ключових факторів:
- Тип оптичного волокна. Переконайтеся, що обрана модель підходить для конкретного виду волокна, з яким ви працюєте (наприклад, одномодового або багатомодового).
- Діаметр волокна. Переконайтеся, що прилад здатний працювати з діаметром оптичного волокна, який ви використовуєте.
- Точність сколювання. Важливо, забезпечити високу точність сколювання, щоб мінімізувати втрати сигналу.
- Простота використання. Обирайте пристрій, з яким вам зручно працювати, і який не вимагає складного налаштування. Це особливо актуально для користувачів-початківців.
- Продуктивність. Врахуйте частоту сколювання, яка вам буде потрібна. Не всі прилади призначені для масового застосування.
- Надійність і довговічність. Перевірте відгуки та репутацію виробника, щоб переконатися в надійності та довговічності.
- Безпека. Зверніть увагу на заходи безпеки, включно з наявністю захисних механізмів, які запобігають випадковим травмам під час використання.
- Ціна і бюджет. Підрахуйте свій бюджет і обирайте відповідно до ваших фінансових можливостей. Ймовірно, що в дорожчих моделях є функції, без яких ви зможете працювати. А може бути й ні.
- Підтримка та обслуговування. Дізнайтеся про доступність технічної підтримки та наявність запасних частин, щоб у разі потреби забезпечити його обслуговування.
Неправильний вибір може суттєво вплинути на якість роботи та рівень втрат сигналу, тому слід провести ретельний аналіз ваших потреб і можливостей перед покупкою. А якщо ви заплуталися або не впевнені у виборі - ми завжди з радістю готові надати безкоштовні консультації щодо вибору!